Guitar build journal
Week 1
For this first session we will make the body template, the work board with side adjusters, and the shim that supports the top when it is clamped to the work board. We’ll make a jig to aid in cutting the scarf joint for the neck on the table saw. Bring a pair of scissors to cut poster board for templates.
Week 2
What you need to bring:
Neck material – 2 pieces of Mahogany 3” x ¾” x 24”
Headstock veneer – cocobolo the piece that is approximately 3” wide x 7” long
Top – Sitka spruce
Back – Rosewood
Sides – Rosewood
Truss rod
2 - Cross dowel nuts and screws
Plywood that we cut as an extra leg of the workboard
Bring the template for the body that you made
Look at page 71 for a template for the headstock. You can use this or you can design your own. Just keep the dimensions within the bounds of the headstock.
Look at this web site and pick out which style initial you want to inlay into the headstock. One of the 9/16” tall letters would look good. If you want something simple to inlay, look at the circles with an initial. They are $30.00 as opposed to $6.00 for a simple letter. I’ll need to get this ordered next week.
http://luthiersupply.com/Pearl-Letters-Many-Styles.html
If you have or can get an old inner tube that we can cut into strips to wrap odd shaped pieces that need to be clamped, bring them.
You won’t need the workboard or the workboard shim this week.
We’ll start with the neck (chapter 4). You have 2 mahogany boards that need to be dimensioned to 3” wide and ¾” thick. In step 2 in the book he cuts the scarf joint with a hand saw then makes the angled surfaces true in step 4. I make a simple fence set to 15 degrees to fit the miter slot in the table saw which gives me a surface that is very close to ready to glue. We’ll make that jig as one that everyone will use.
In step 4, I use the bandsaw to reduce the headstock thickness to ½”.
Bring the plywood (extra leg) to use in clamping and gluing as in the picture in 4-8.
We’ll cut and glue the stacked heel block.
We’ll skip making your own truss rod since we bought those.
You have a piece of cocobolo to use as the headstock veneer. It will need to be dimensioned to around 1/16” thick and glued to the headstock (page 63) although you won’t glue it until you slot for the truss rod.
Page 58 – if the neck blank has time for the glue to dry we’ll pick up with this procedure.
While the neck is drying we can begin to join the top, back and sides and glue the top and back bookmatched halves.
It’s not likely that we’ll get to page 80, carving the heel but we’ll look at how this is done.
Week 3
This week you can go ahead and glue the heel to the neck shaft. Refer to page 48 Step 8. The line you marked and sanded to on the peghead is the starting line for the measurements. If you don’t get the heel glued you can do that first thing.
With this done Monday we can:
Cut the slot for the truss rod (page 58)
Cut the tenon on the heel block (page 59- 61)
Drill the tenon and head block to mate together (refer to bolt on neck https://www.cumpiano.com/an-improved-neck-body-joint)
Apply the headstock (peghead) veneer (page 63)
We’ll then switch our attention to the top that you glued:
Cut the top to the template plus about ¼” overhang
Dimension the top to between .1 and .125 thickness (page 104 – 112) We’ll use the drum sander rather than hand plane
Install the rosette that you purchased (page 124 – 126 and page 133) We’ll match the channel to the purchased rosette.
You’ll also join and glue the back like you did the top
If we get all that done we’ll be doing good.
What you will need:
Workboard but not the dowels.
The ¼” drill bushing to be installed in the workboard at the center of the soundhole
Neck with heel block
Truss rod
Peghead veneer (cocobolo)
Head block (that’s the mahogany that we cut a mortise )
Barrel nuts and bolts (2 of those)
Top
Rosette (package contains 3 rings)
Miscellaneous:
It’s a good idea to have a small bottle of CA glue in case of a repair (yes that happens)
Start gathering spring clamps that you will need later. Home Depot has the 2” clamps for $.99 and the ¾” for $.47. I use the 2” for clamping the sides to the dowels and the ¾” for clamping the kerfing to the sides
You’re going to need cam clamps to clamp the bracing to the top and back starting in week 4 Look at page 159 and you’ll see what I mean). We have 6 clamps at the WEC and I have some you can use. You may be able to borrow some from the folks who built mandolins. I’ve attached a plan if you want to build your own.
A good sharp chisel will be needed to carve your braces. We have some at the WEC but it’s good to have your own and get used to using them.
Week 4
Meeting June 4th
We’ll pick up from where we left off Monday and finish cutting the sound hole on the top. Go ahead and clean up the top and put a light coat of finish (lacquer, varnish, true oil, etc) to help protect it from damage as we keep working on it.
At home make the following:
Fingerboard template using the left over poster board. See page 38 for the steel string layout. It’s kind of hard to follow with both SS and CL in the text so here’s the SS:
A-B 25.4” Scale length
A-C 25.55” Compensated scale length
A-D 26.05” Nut to bridge pin
A-K 14-3/32” Location of 14th fret also the neck to body location
E-F 2-1/8” Outside string measurement at the bridge
G-H 1-11/16” Width of fingerboard at the nut
I-J 1-7/16” Outside string measurement at the nut
N-O 2-1/4” Fingerboard width at the 14th fret
A-P 17-27/32” Length of fingerboard
A-S 19-31/32” Nut to center of soundhole
Headplate clamping caul ¾” thick 6-3/4” long X 3” wide and glue cork to one side
Headplate template in poster board see the one on Page 71 or a similar design
Clamping shoe – page 36 put cork on one side
On Monday we will work on the following:
On the neck we will:
Page 50 - steps 11 and 12 trim the heel block and layout the shaft
Page 58 – Truss rod slot and neck tenon
Page 62 – Installing the truss rod
Page 63 – Applying the headstock (peghead) veneer
On page 64 we’ll use the table saw technique
Page 70 – Cutting the headpiece outline
Page 74 – drilling the steel string headpiece.
Page 80 – Carving the heel
Look ahead to page 143 on Soundboard bracing
While glue is drying you can:
Page 147 – prepare brace blanks
Layout the bracing (page 153)
Cut your back to the template
Thickness sand the back and sides
Material needed:
Neck
Truss rod
Headstock veneer
Mother of Pearl Initial
Tuning machines
Brace material (spruce)
Top
The scrap pieces cut from your top
Back & Sides
Scrap of wood ¼” – ½” thick X 3” wide X 6” long
Tools needed:
“C” clamps if you have some
Body template
Fingerboard template (made at home)
Headplate template (made at home)
Headplate caul (made at home)
Chisel for carving (1/2” paring chisel works good for carving)
Rasp and files
Carving knife or skew chisel (see page 91)
Scraper
We’ll make a template for the top arching of 27’ radius and the back arching of 10’8” radius described in step 4 on page 150.
Week 5
Meeting June 11
At Home:
Plane the spline, you installed over the truss rod, flush with the neck shaft.
Glue the headstock veneer to the headstock (page 64). We will trim it on the table saw as in the picture 4-28.
Draw the outline of your headstock on the back side of the headstock so you can bandsaw it with the headstock flat on the bandsaw table.
Look at picture 4-39 on page 71 to see how the tuning machines need to be spaced but your pattern doesn’t have to look like this.
Make 3 templates – The heel cap on page 81; The heel side profile on page 82;The heel end profile on page 87
On Monday we will work on the following:
Page 72 - Sawing the headstock outline to your pattern
Page 74 Drilling for tuning machines
Drill the neck and headblock to accept the barrel nut and screw. This is from book updates on Cumpaino’s web site https://www.cumpiano.com/an-improved-neck-body-joint
Page 80 – 91 - Carve the heel
We should have time to bend sides for 2 guitars so we will prepare the sides (step 7 & 8 page 101) joint one edge of the sides, rip to just over 4” about 1/16” and sand your sides to .085” (page 104).
You can sand your back to .10 (page 104).
A note about sanding rosewood”: It is very oily and will gum the sander quickly so clean the sanding belt with each pass and take small passes (about 1/8 turn). Check frequently to be sure not to ruin a back or side.
For those who finish carving their neck heel, you can start preparing your braces (page 147 – 152).
A sanding block cut to an arch to match the arch of the top (27’ radius) and another to match the arch of the back (10’ 8”) (page 150) work great for arching the braces. I start with a piece of 2” wide and 20” long and cut the arch on the bandsaw then use double side tape to hold a strip of sandpaper.
Material needed:
Neck
Barrel nut and screw
Tuning machines
Back & Sides
Brace material
(2) 2” x 2” x 20” scraps of wood for sanding blocks
Tools needed:
Chisels
Rasp & files (a 4 way rasp works pretty well)
Work board with dowels (if you might be bending your sides)
2” spring clamps to clamp sides to dowels on workboard
Soundhole center you cut from soundboard (for a template)
Week 6
Meeting 6/17/18
This week we’ll start bracing the top and adding kerfing to the sides.
At home try to complete the following:
Finish cutting the headstock to your shape
Clean up the heel with moderate grit sandpaper. You’ll sand to final later.
Refer to the chapter on Soundboard Bracing (page 143). Get familiar with the picture on pages 149, 151 and 154
Lightly draw the bracing on the inside of your top. You marked their location on your body template. Also refer to page 154.
Material you need to bring:
Work board with sides
Top
The left over pieces from where you cut the top (we’ll use some of it for braces)
Brace material (spruce boards)
Mahogany 1” x 1” sticks (to make kerfing)
Material to make arch template (step 4 page 150) We have some 1/8” plywood we can use for this.
Material to make sanding sticks to match the arch (A couple scrap pieces of 2” x 2” x 20” should be fine)
Cork to make some clamping cauls
I’ll bring some scraps of ½” plywood to make the Bridge Patch Caul (page 165)
I have the material for the bridge patch
Scrap of 1” x 1” x 12” to make the Upper Transverse Graft caul (see the picture on page 166)
¾” plywood left over from making the workboard – you’ll need a piece about 12” wide and 20” long to make a sanding board
Tools and templates you need to bring:
Body template
Poster board with cork shim
Cam Clamps - (Let me know if you need me to bring some)
1” clamps to clamp the kerfing to the sides – clothespins reinforced with a rubber band will also work. You need around 25 per side.
Week 7
Meeting 6/25/18
At Home:
Finish gluing the flat braces (Upper transverse graft, Sound hole brace, Finger braces, Bridge patch)
Check and trim the edge of the bridge patch so that the x brace will lie against it and on the line you drew.
Using the x brace mark the end of the Sound hole brace and cut flush to the line (page 169)
If you feel comfortable with shaping the flat braces go ahead. If you want to wait, you can shape them Monday.
Finish gluing the kerfing to the top of the sides.
On Monday we will work on the following:
NECK
Page 72 - Sawing the headstock outline to your pattern
Page 74 Drilling for tuning machines
Drill the neck and headblock to accept the barrel nut and screw. This is from book updates on Cumpaino’s web site https://www.cumpiano.com/an-improved-neck-body-joint
TOP
Sand the arch on the remaining top braces.
Cut the notch for the x braces (page 170)
Glue the Upper and Lower face braces. (Page 173)
BACK
While glue is drying you can sand the back to .010” Be sure to scrape off the glue prior to sanding.
You can cut and install the back plate centerseam inlay. (Page 221)
Prepare the back braces (Page 223)
SIDES
Make a sanding board and sand the kerfing and sides getting them ready to glue to the top.
Material needed:
Neck and headblock
Barrel nut and screw
Tuning machines
Back & Sides
Top
Brace material
(2) 2” x 2” x 20” scraps of wood for sanding blocks
Large scrap of plywood left over from building the workboard to make a sanding board (I’ll bring the sandpaper and spray adhesive)
Back centerseam inlay
Tools needed:
Chisels – very sharp
Work board with dowels
2” spring clamps to clamp sides to dowels on workboard
Soundhole center you cut from soundboard (for a template)
Cam Clamps
Poster board & cork shim for the top
Week 8
Next Meeting 7/2/18
At Home:
Finish gluing and shaping all the top braces. Refer to the drawing on page 167 for the shapes. Note that the long lower face brace has a height of ½” at the tallest point and the short lower face brace has a height or 3/8” at its tallest point (see page 174).
Cut 3 center seam diamonds from a piece of the left over top and glue and shape them . Their placement is on page 154. Their shape is in reference 7-35 on page 175.
Make a headblock fixture like on page 212. Line up the hole in the fixture with the bottom hole in your headblock. Rather than clamping to the workboard, I drill a hold and use a bolt with a wing nut.
On Monday we will work on the following:
TOP
Glue the headblock to the top (page 194 step 8)
Glue the tailblock to the top (page 195)
Fit and glue the sides to the top (page 205) Be sure to look at the picture on page 207
BACK
Install the centerseam inlay (page 221)
Brace the back (page 222)
FINGERBOARD
Make the fingerboard (starting on page 272) Watch out for what’s done for the classical guitar vs the steel string.
BRIDGE
Make bridge (page 343) I do this a little different than he does it.
Material needed:
Top
Back
Sides
Headblock
Tailblock
Brace material
Back graft material (cutoffs from the top to reinforce the back seam)
Fingerboard blank
Bridge blank
Bone saddle
Bridge pins
Tools needed:
The usual
I’ll bring my trim router to cut the slot in the back for the centerseam and also the slot in the bridge for the saddle.
I have a countersink that works well for making the countersinks for the bridge pins
Fret ruler if you made one – I have a couple extra
I’ll bring my fret saw – I left the miter box at the guild
Final thoughts:
We’re going to have some bottlenecks this week around tools that are being shared so be prepared for everyone to be working on separate things.
I’d like to see everyone get their sides glued to the top if we can.
Once the centerseam inlay is installed on the back you need to get it reinforced with the back graft (page 222)
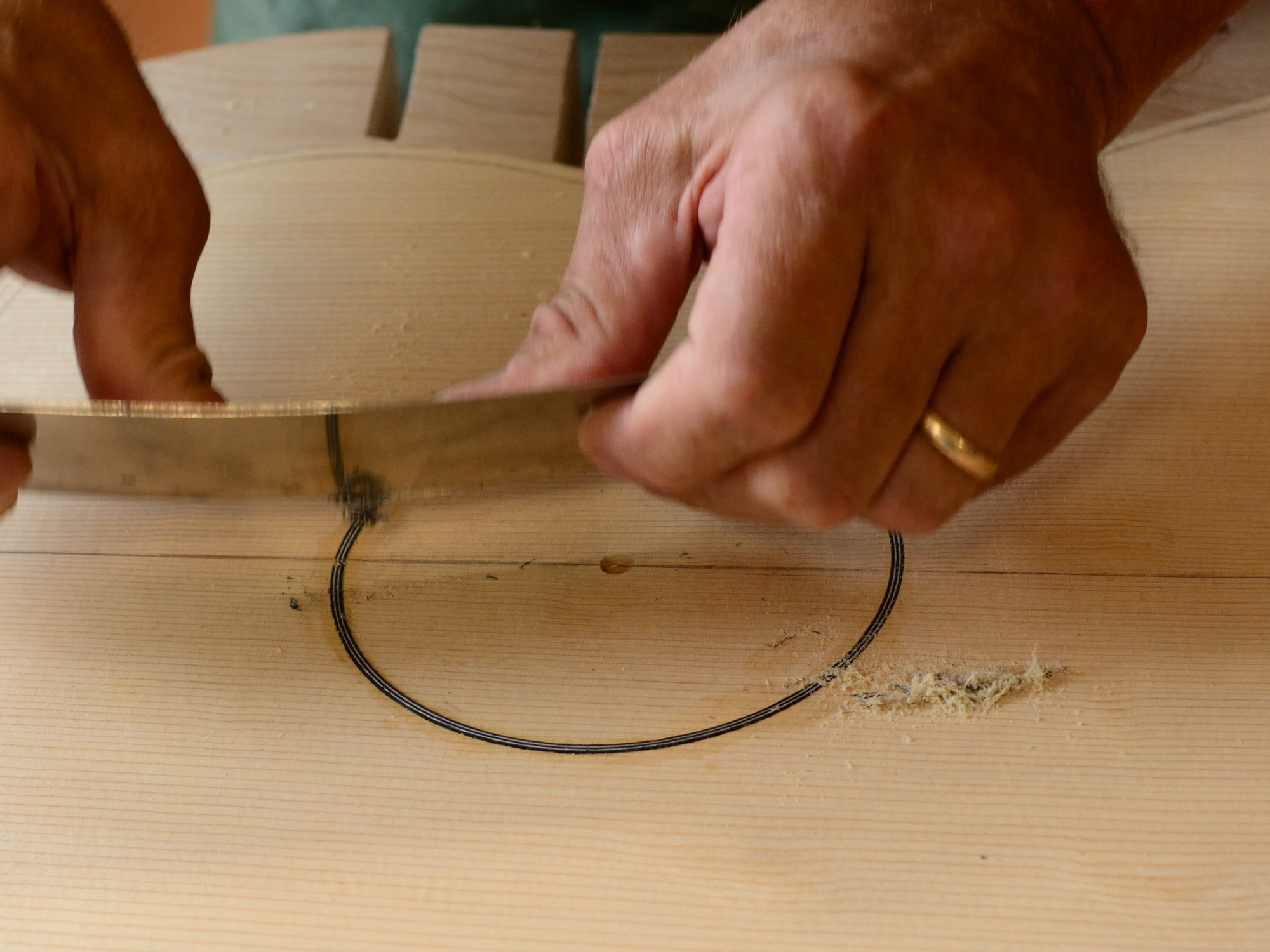
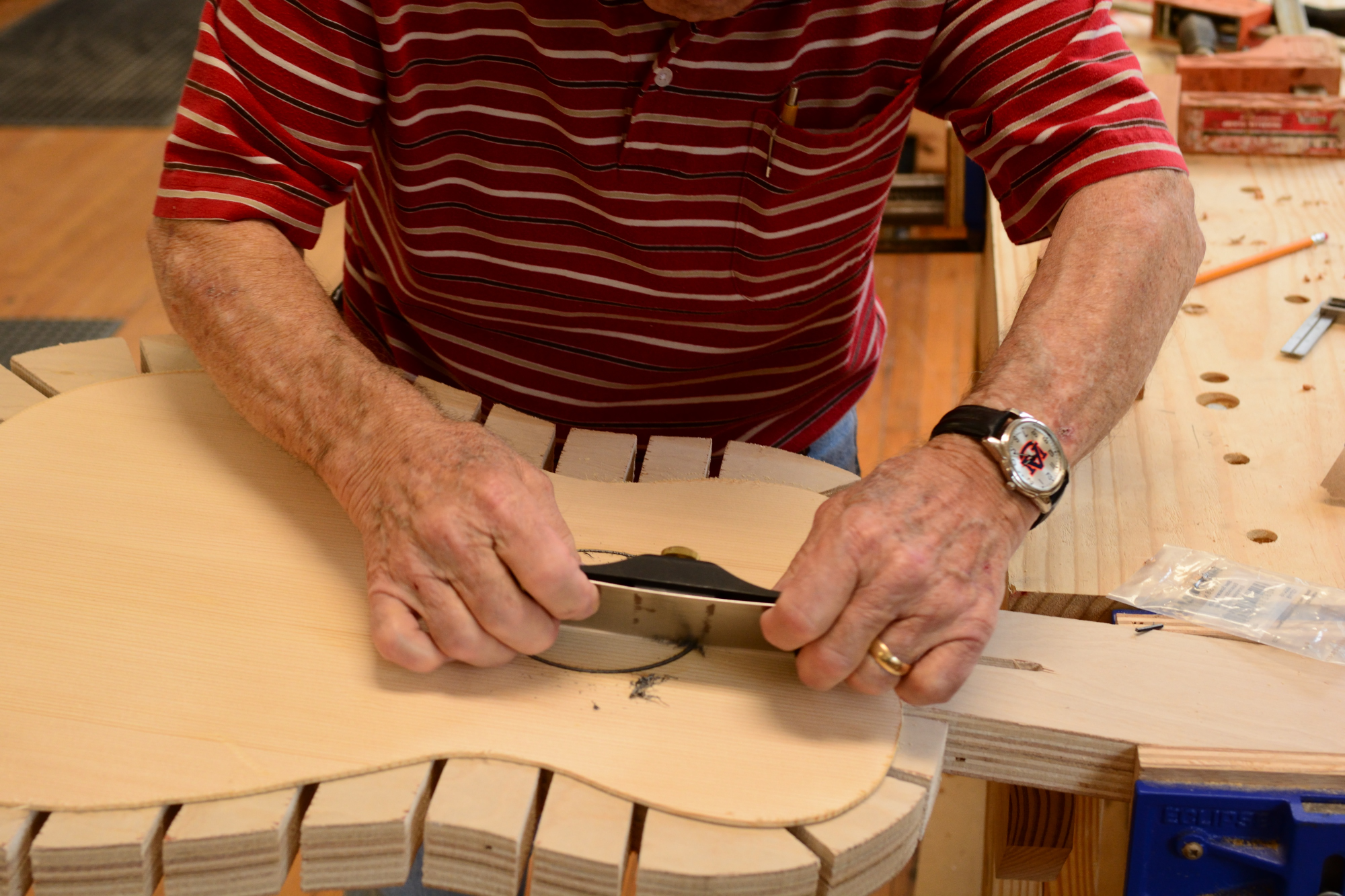
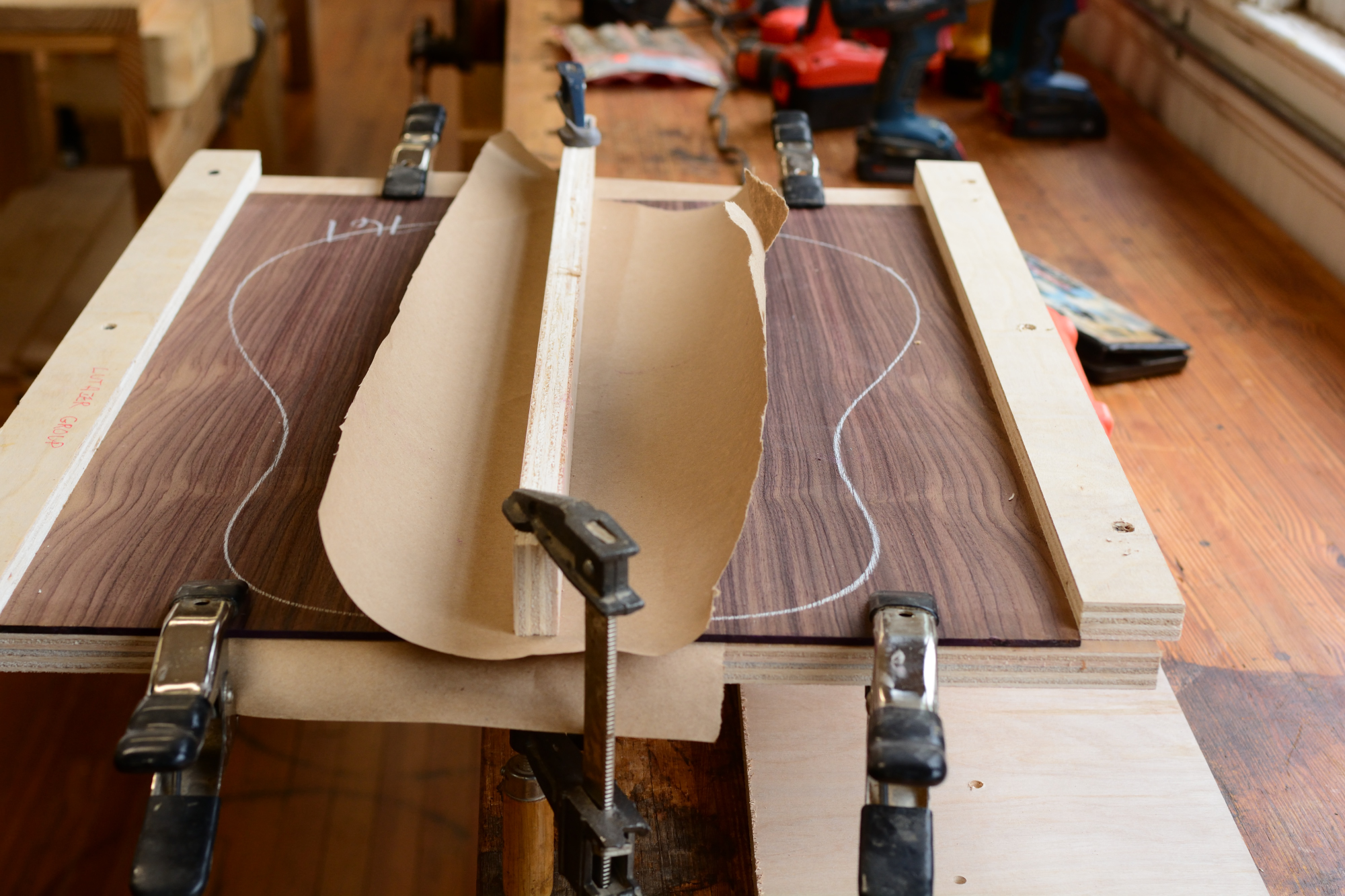
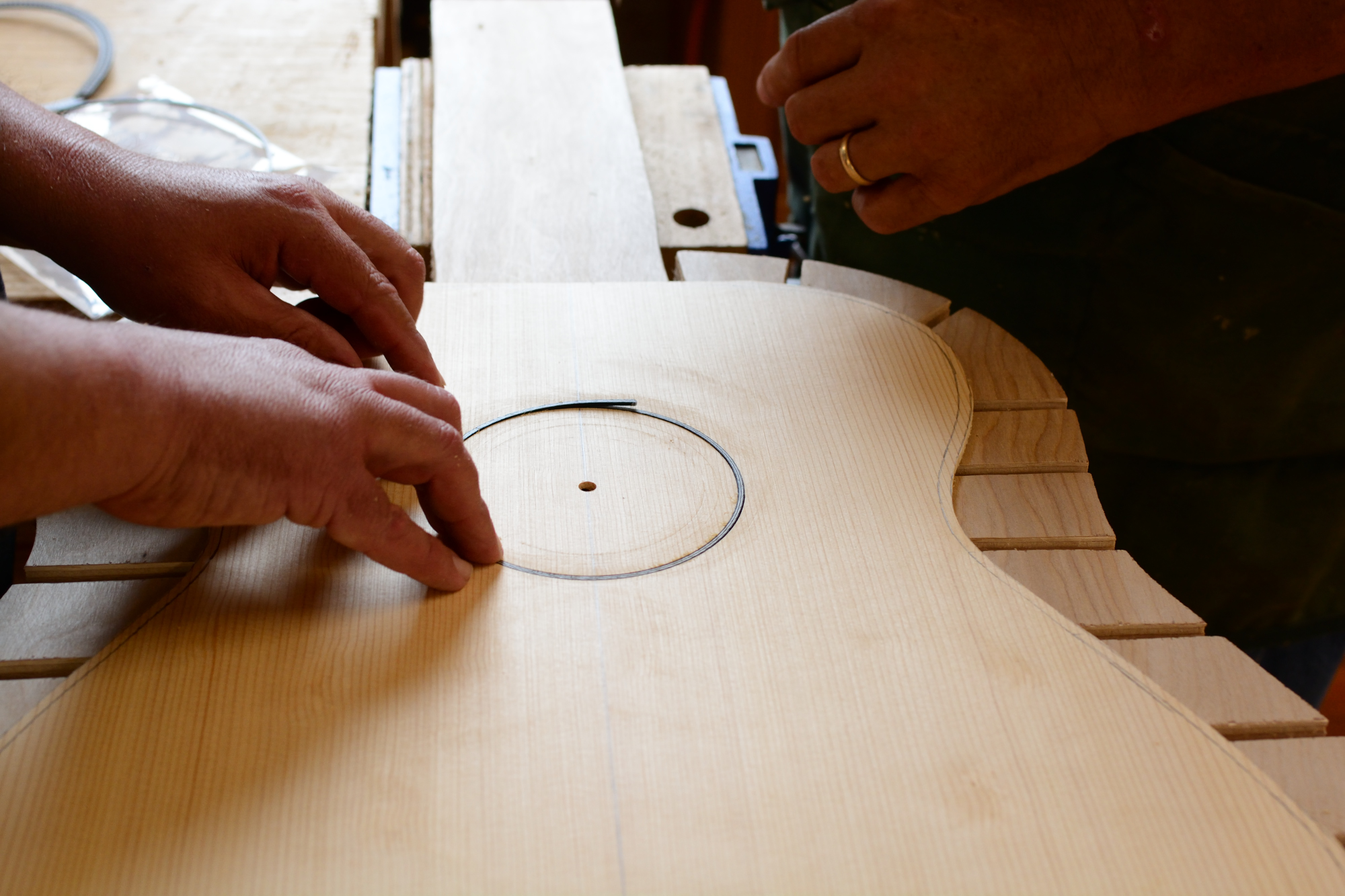
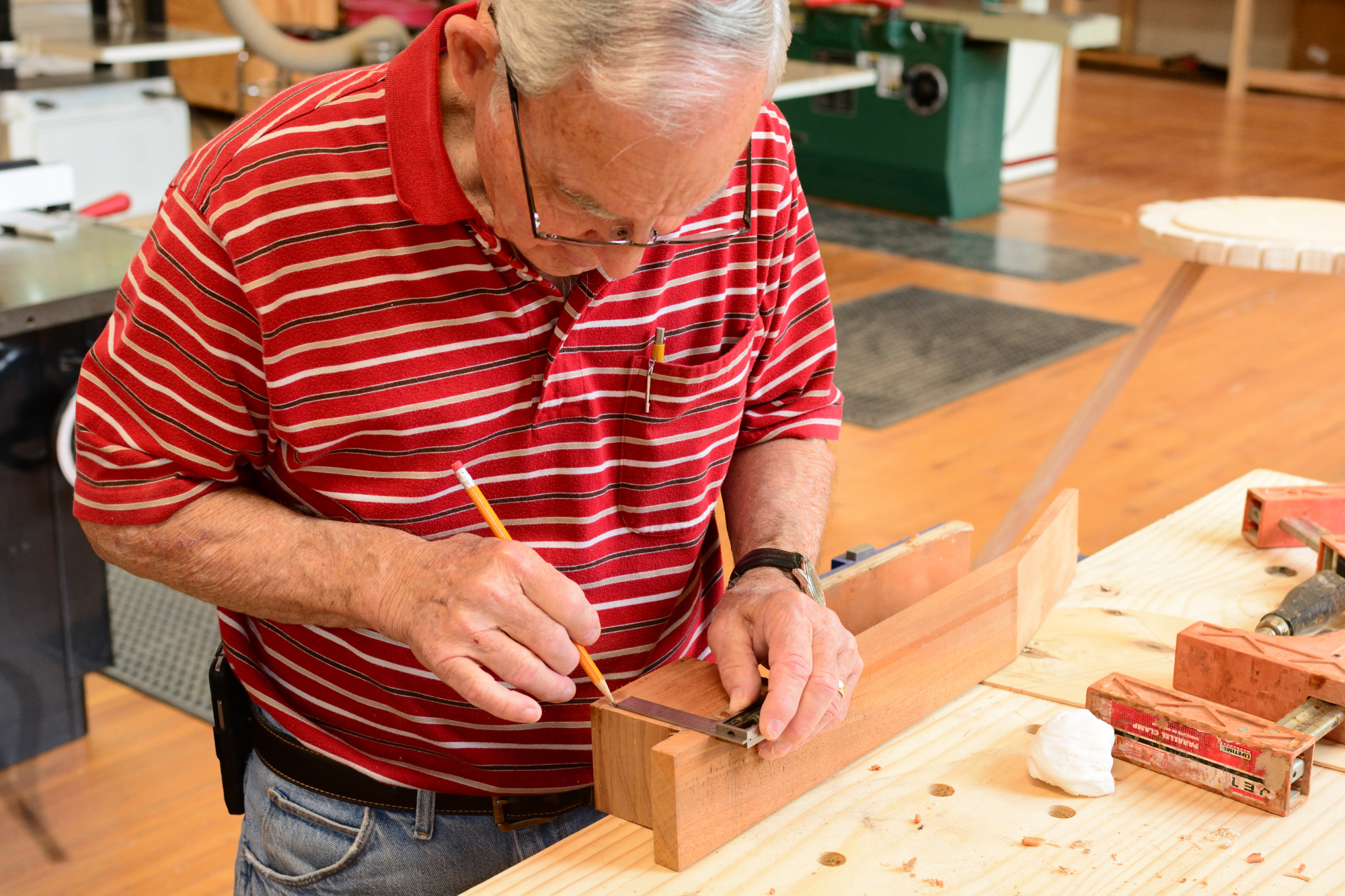
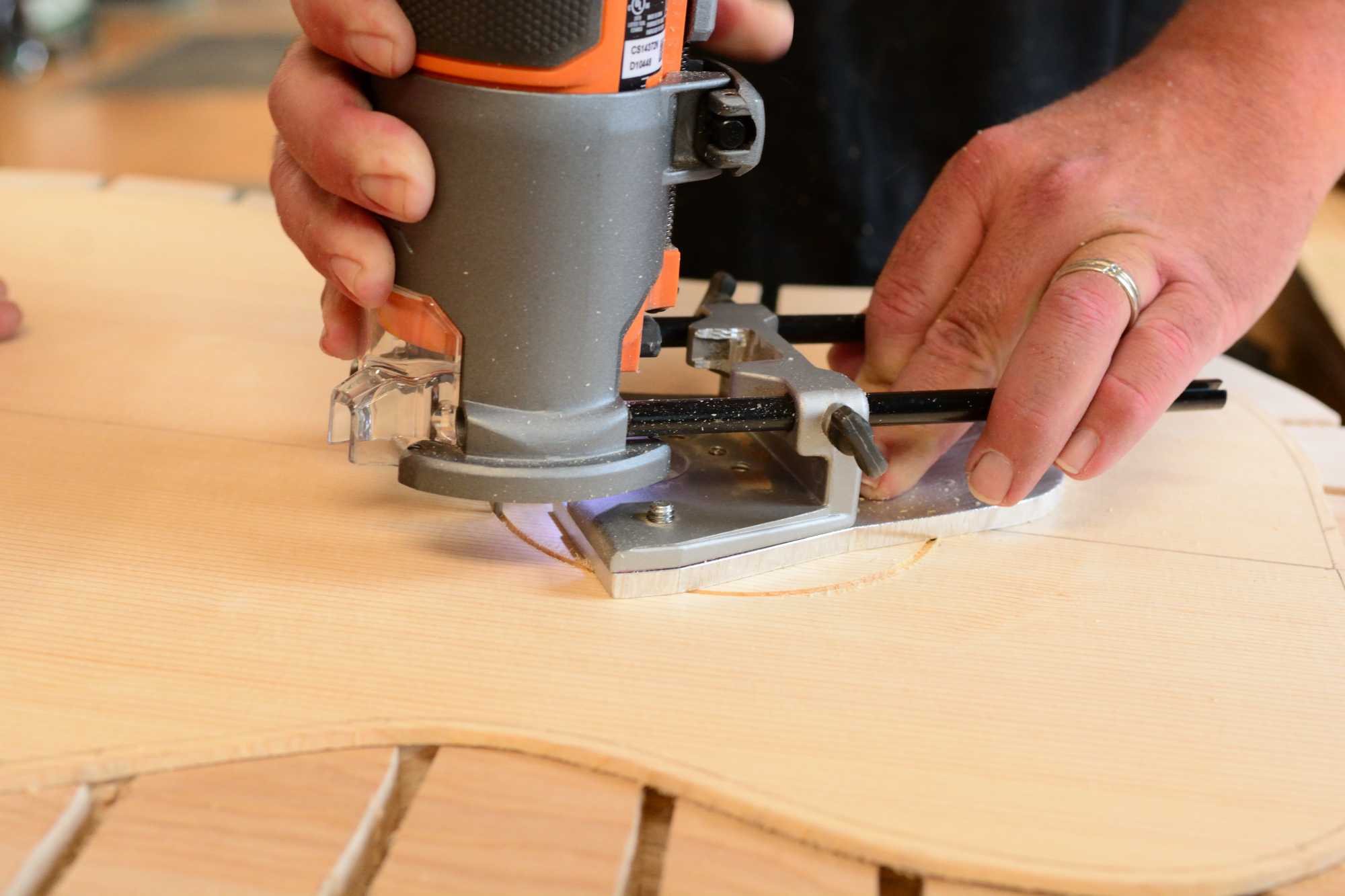
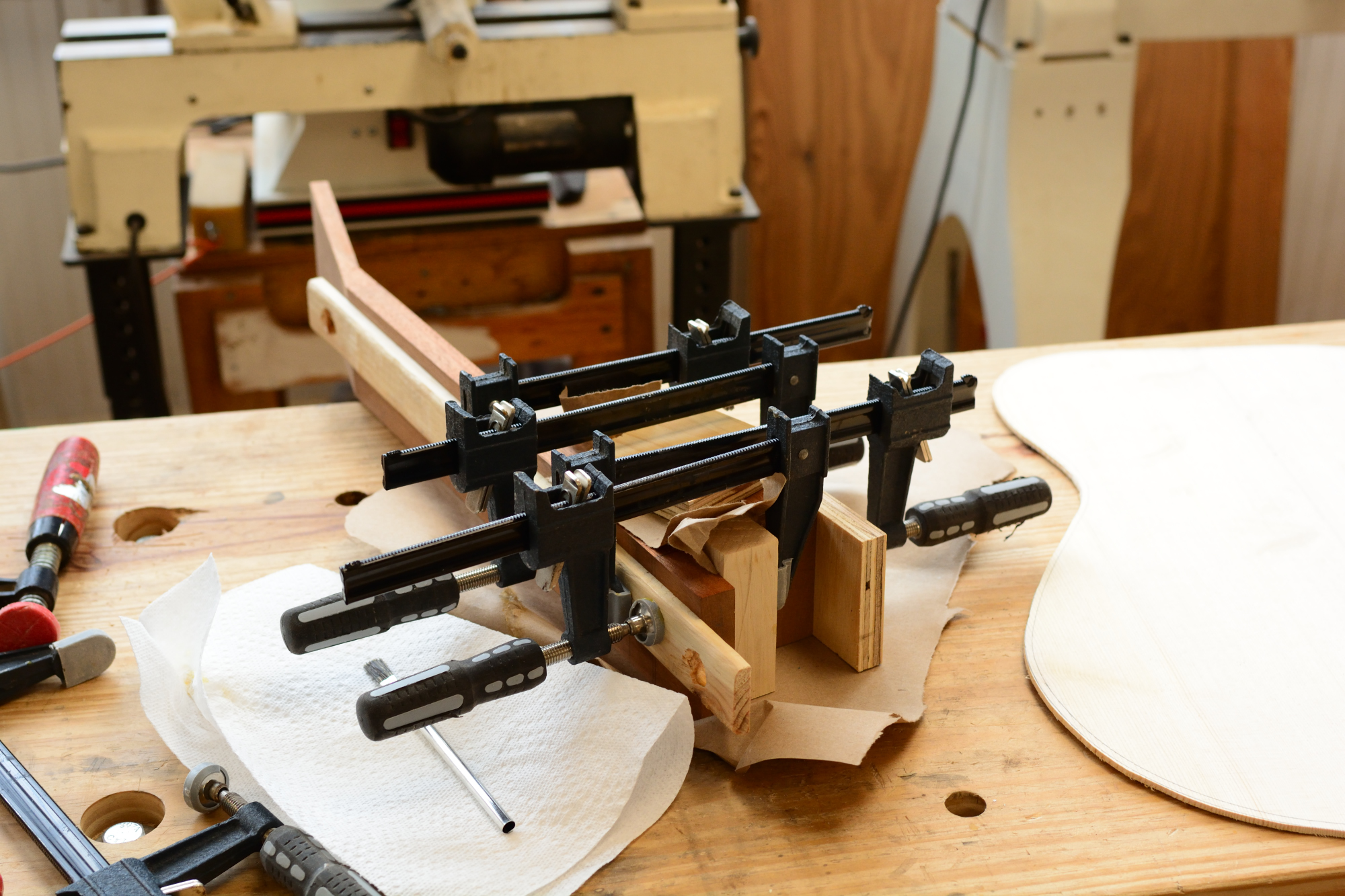
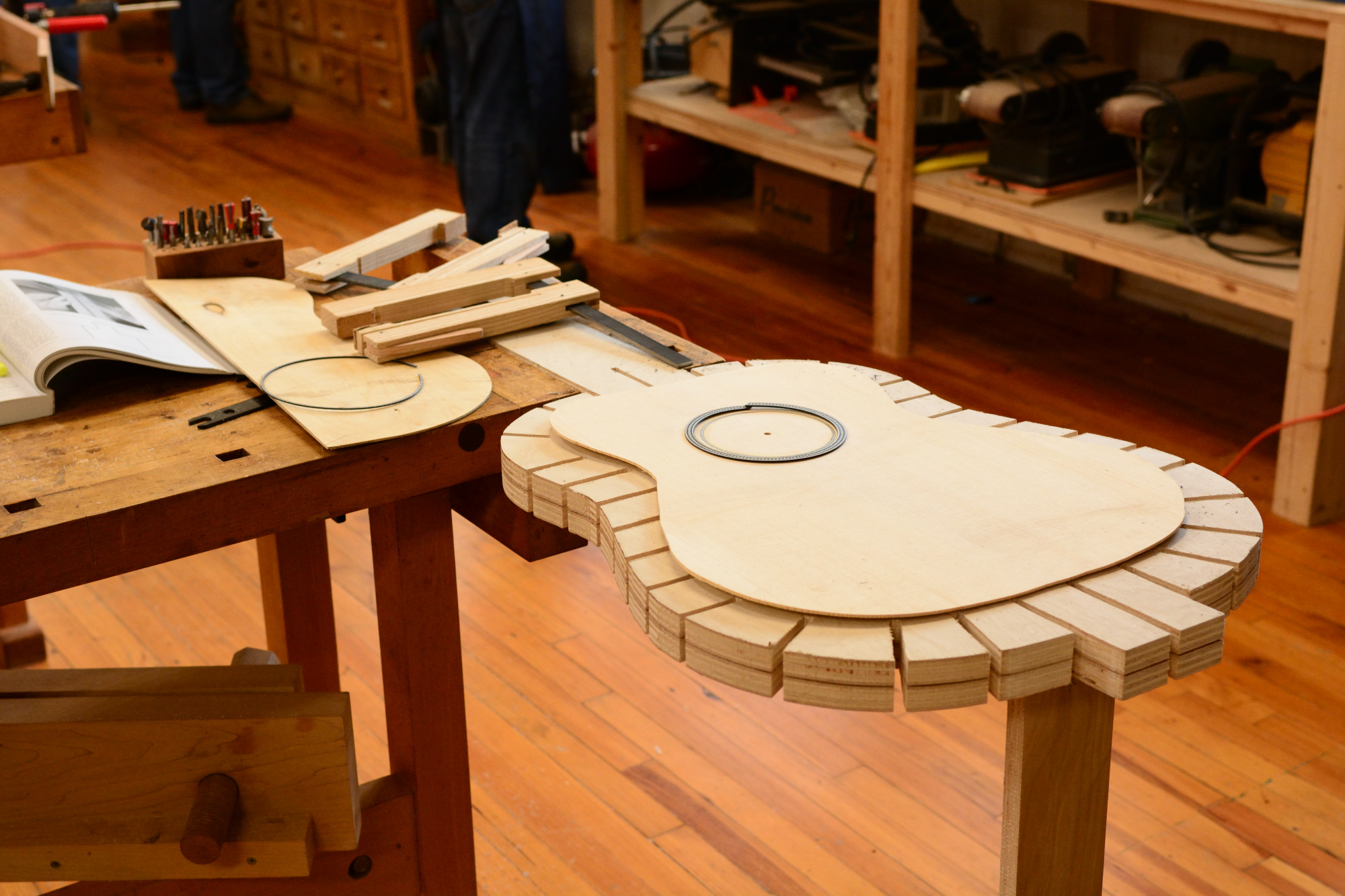
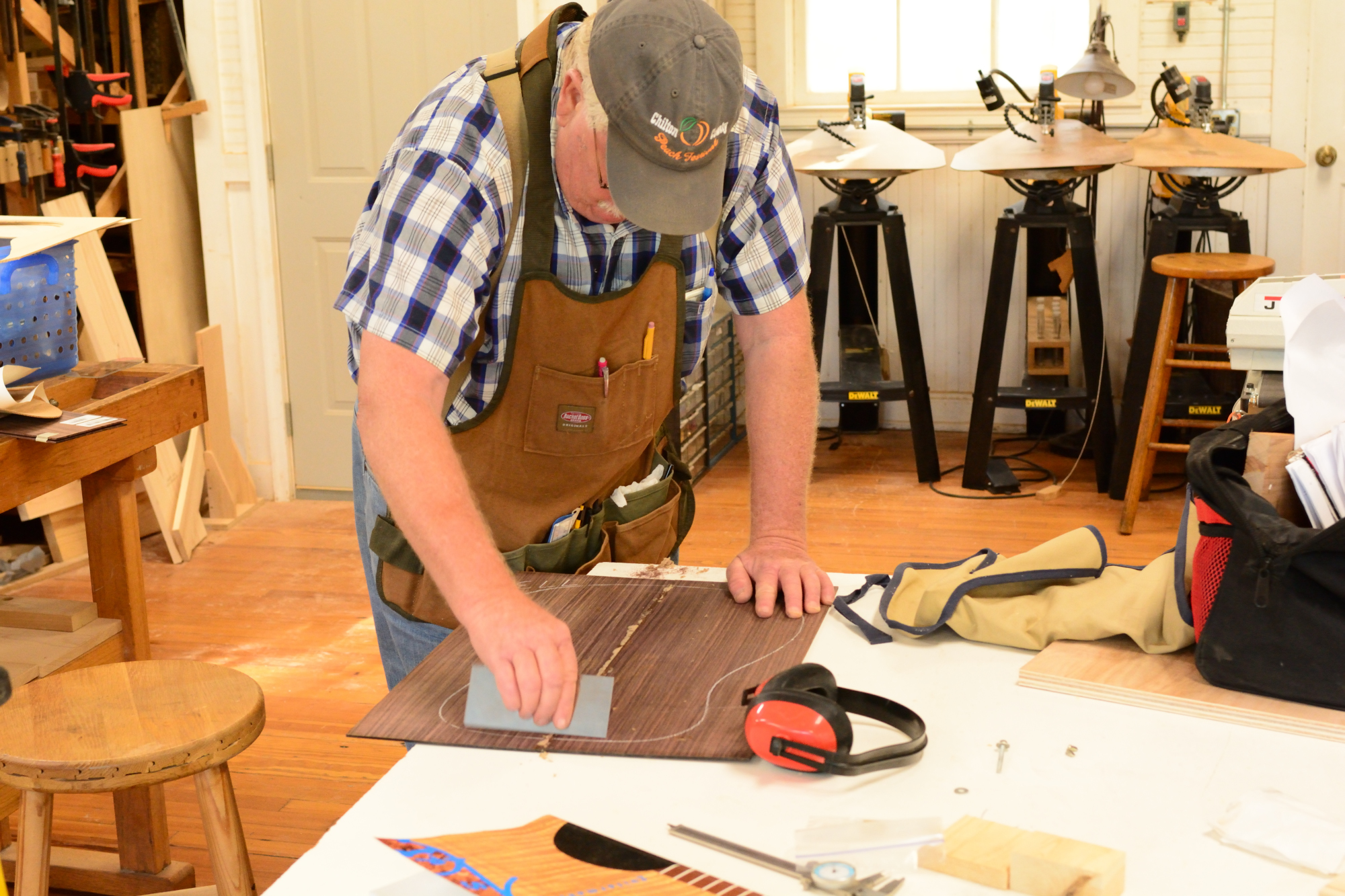
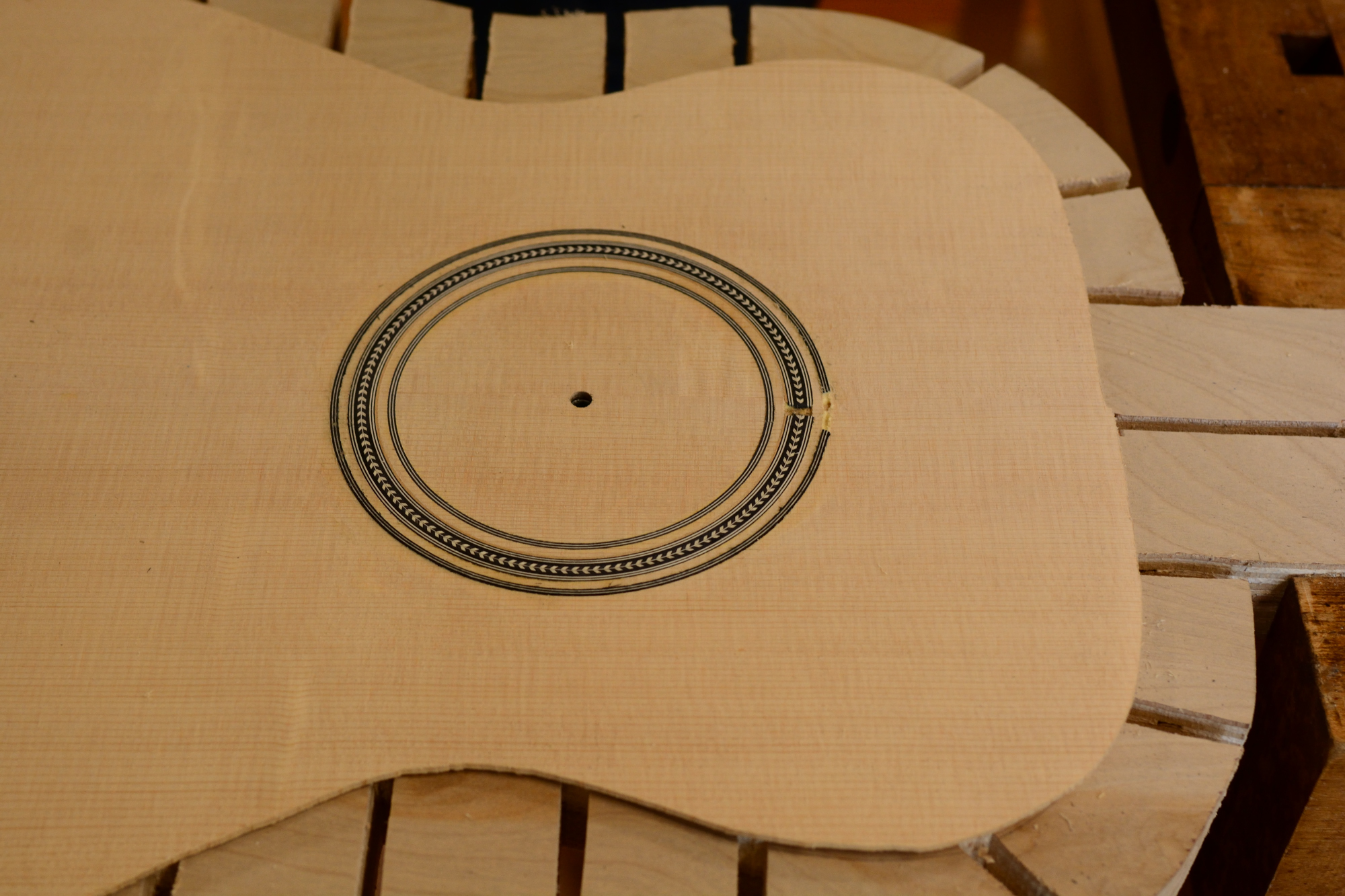
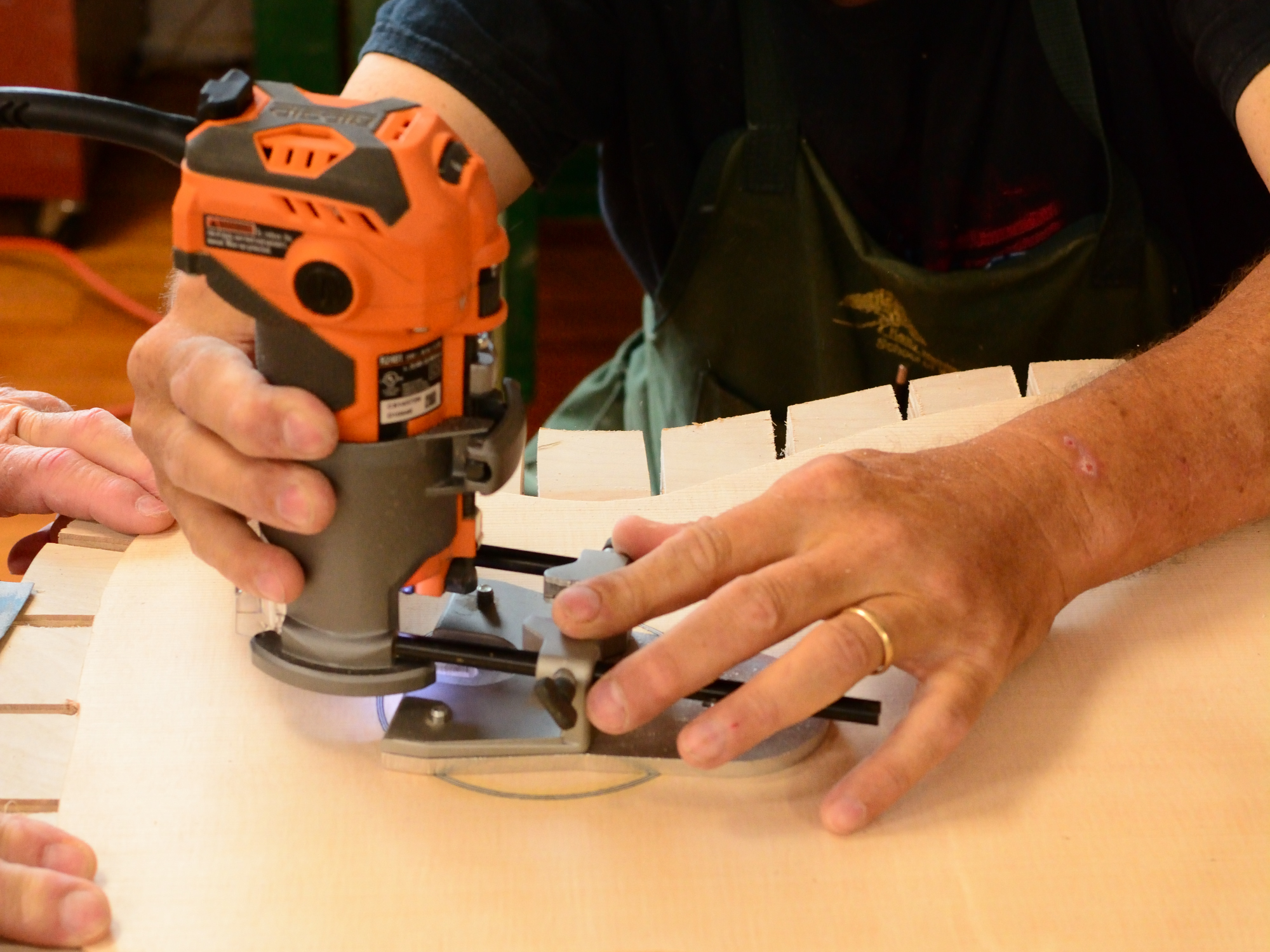
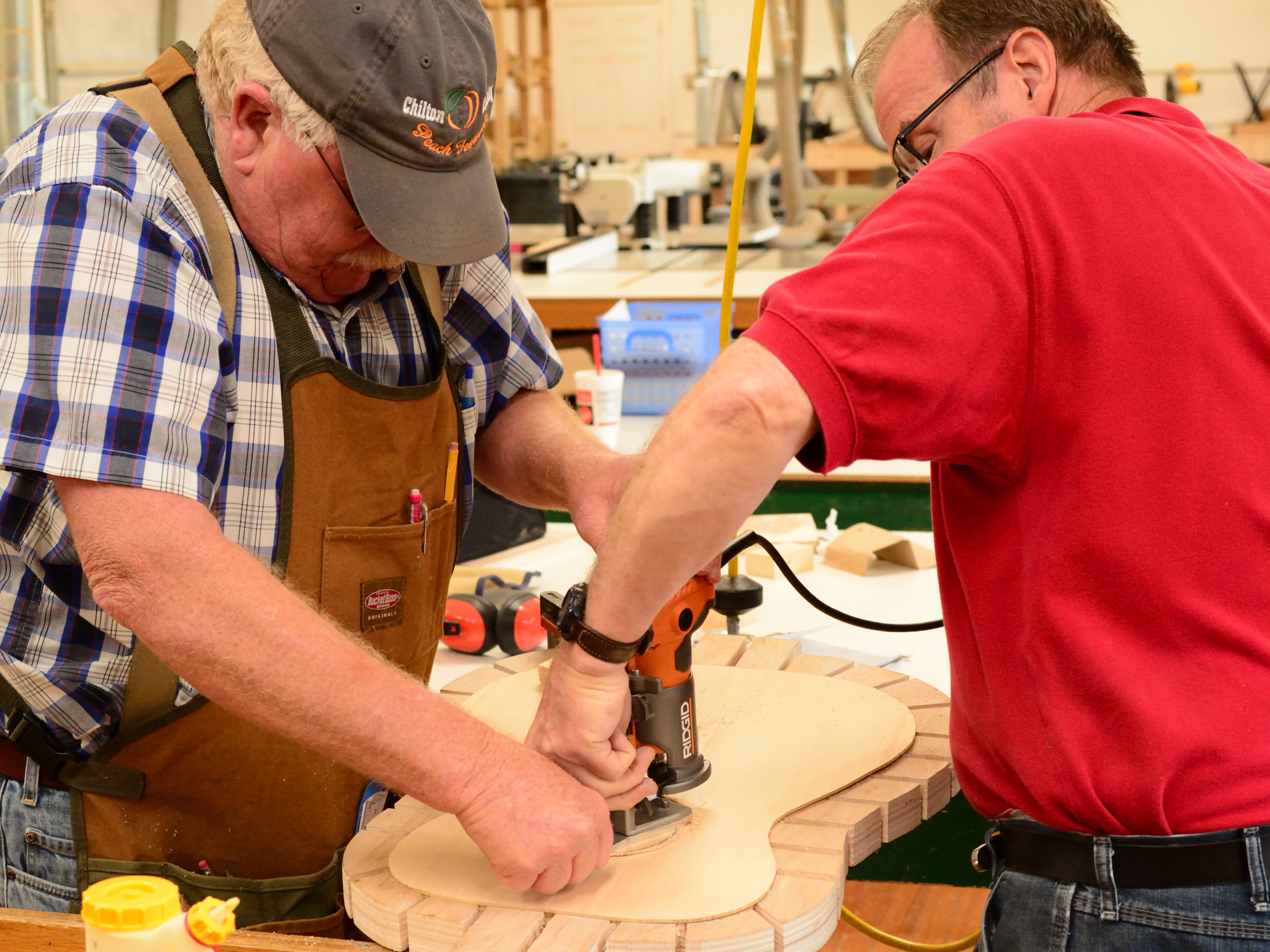
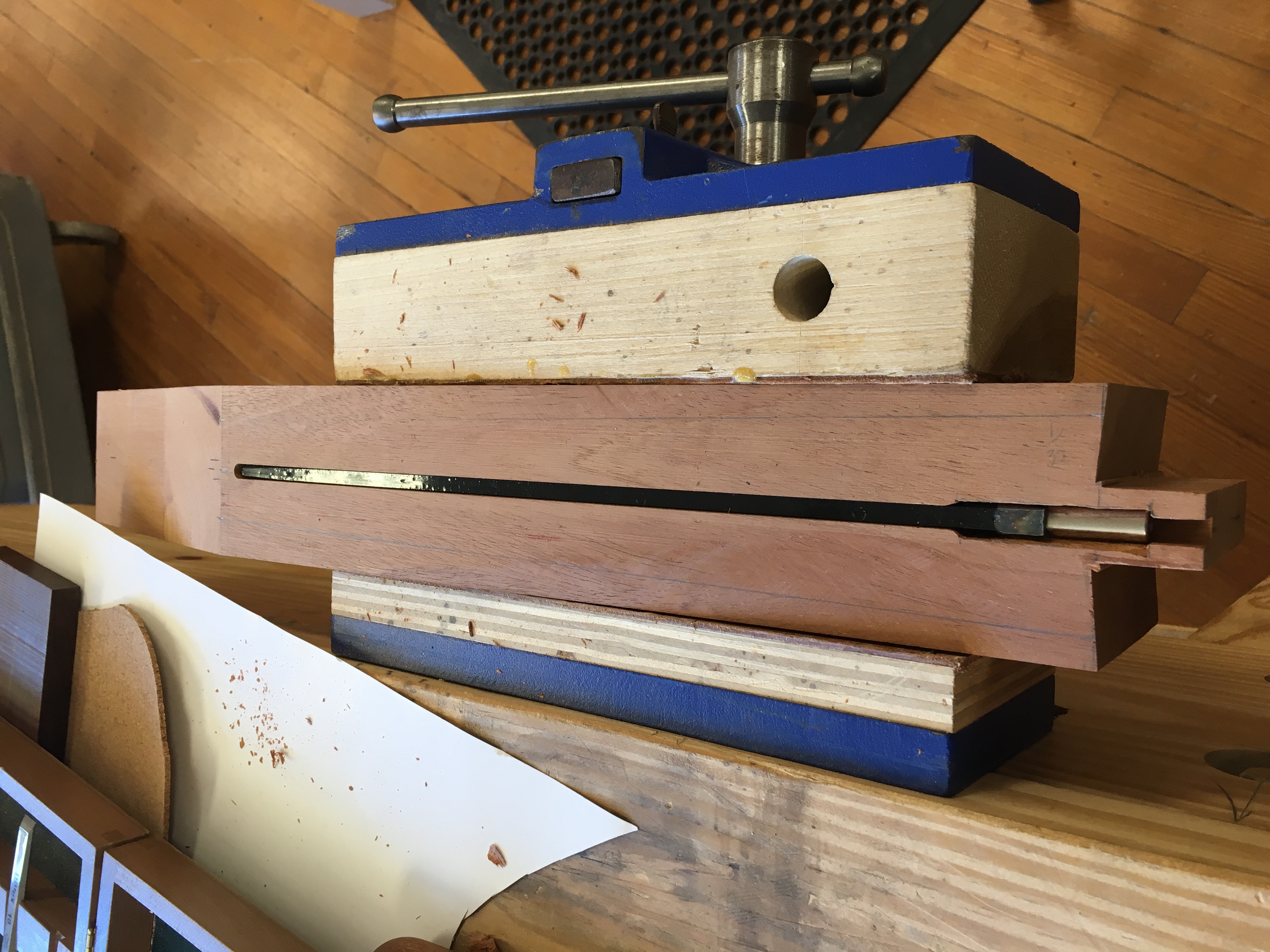
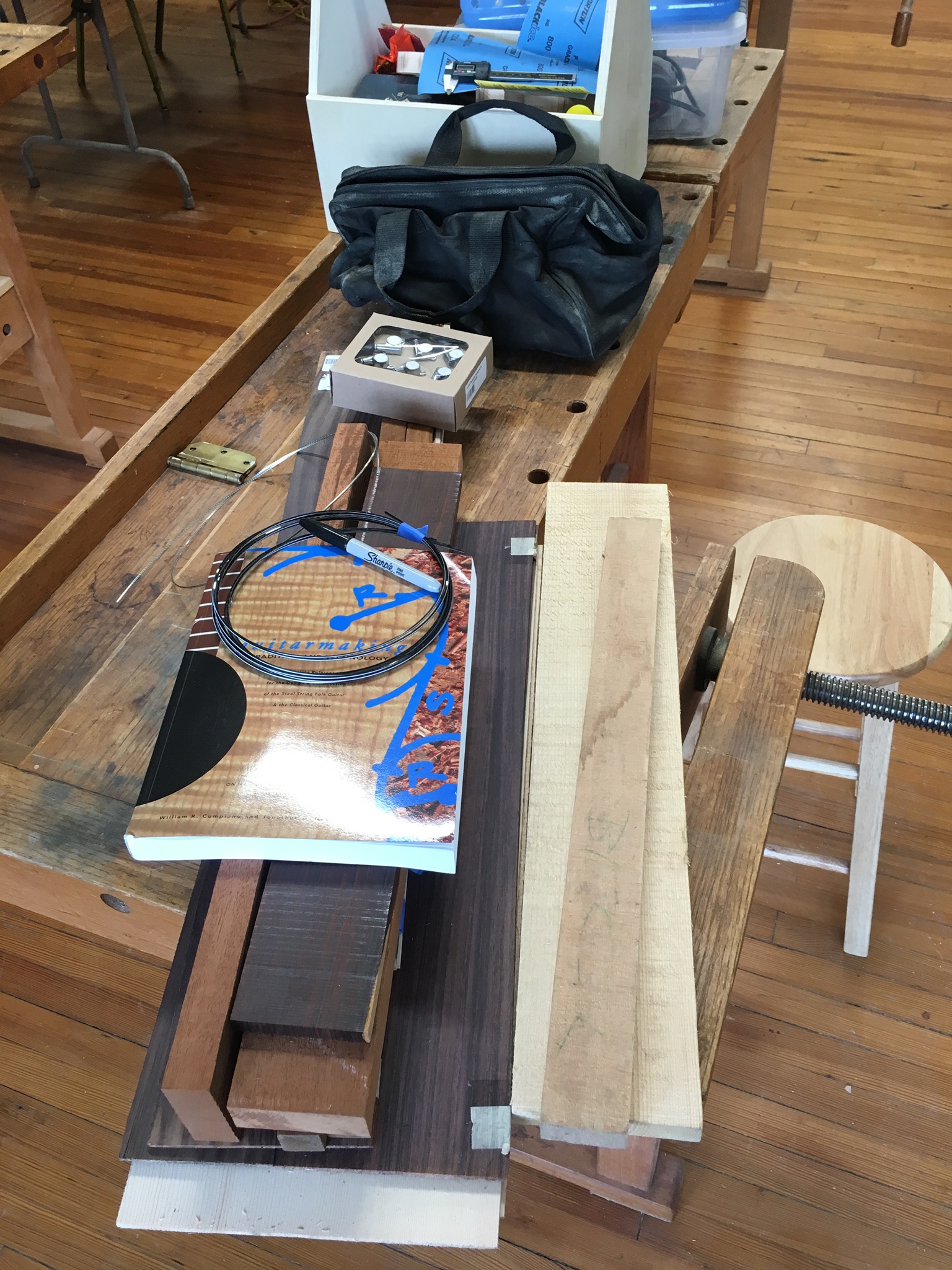
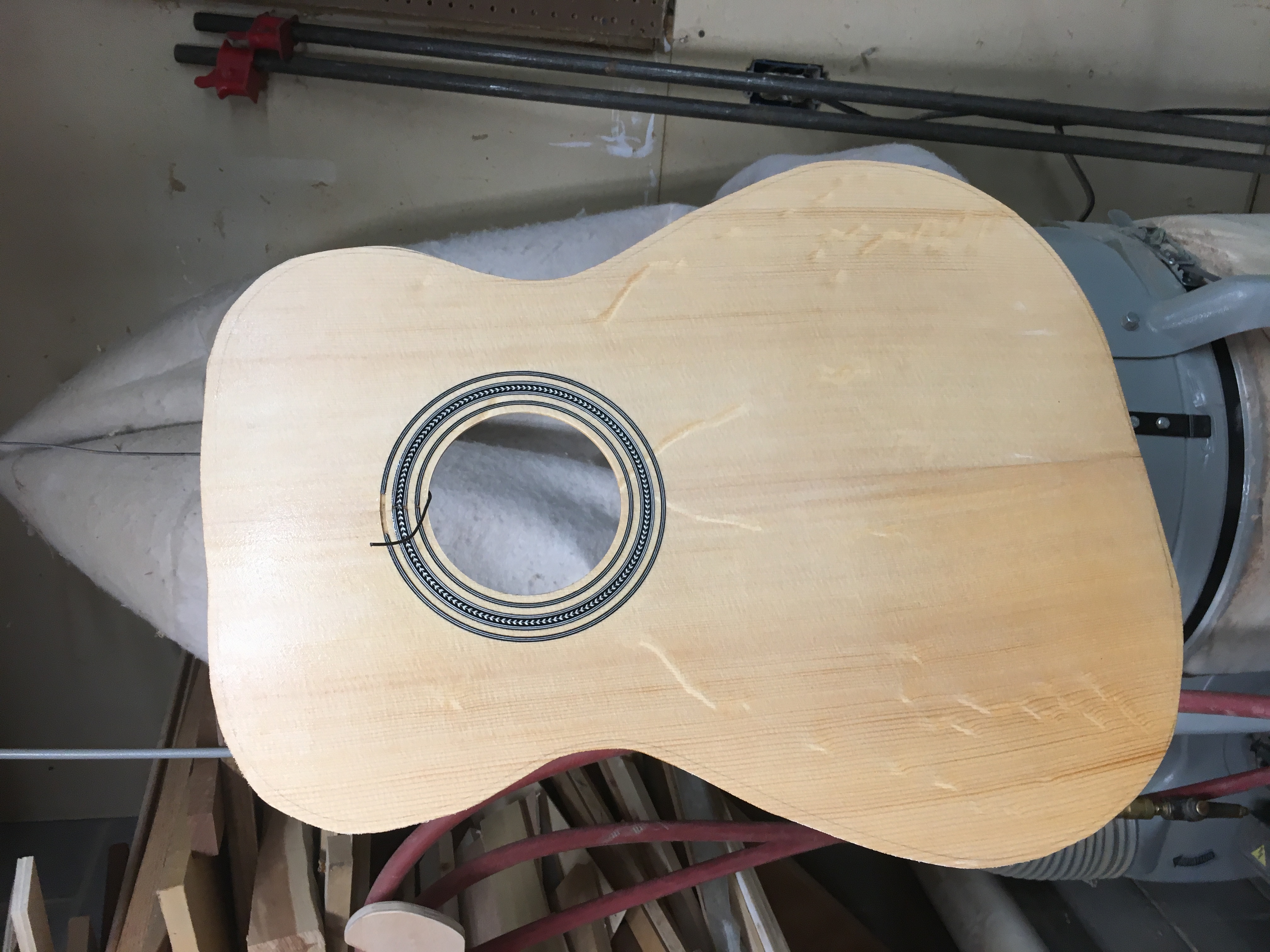
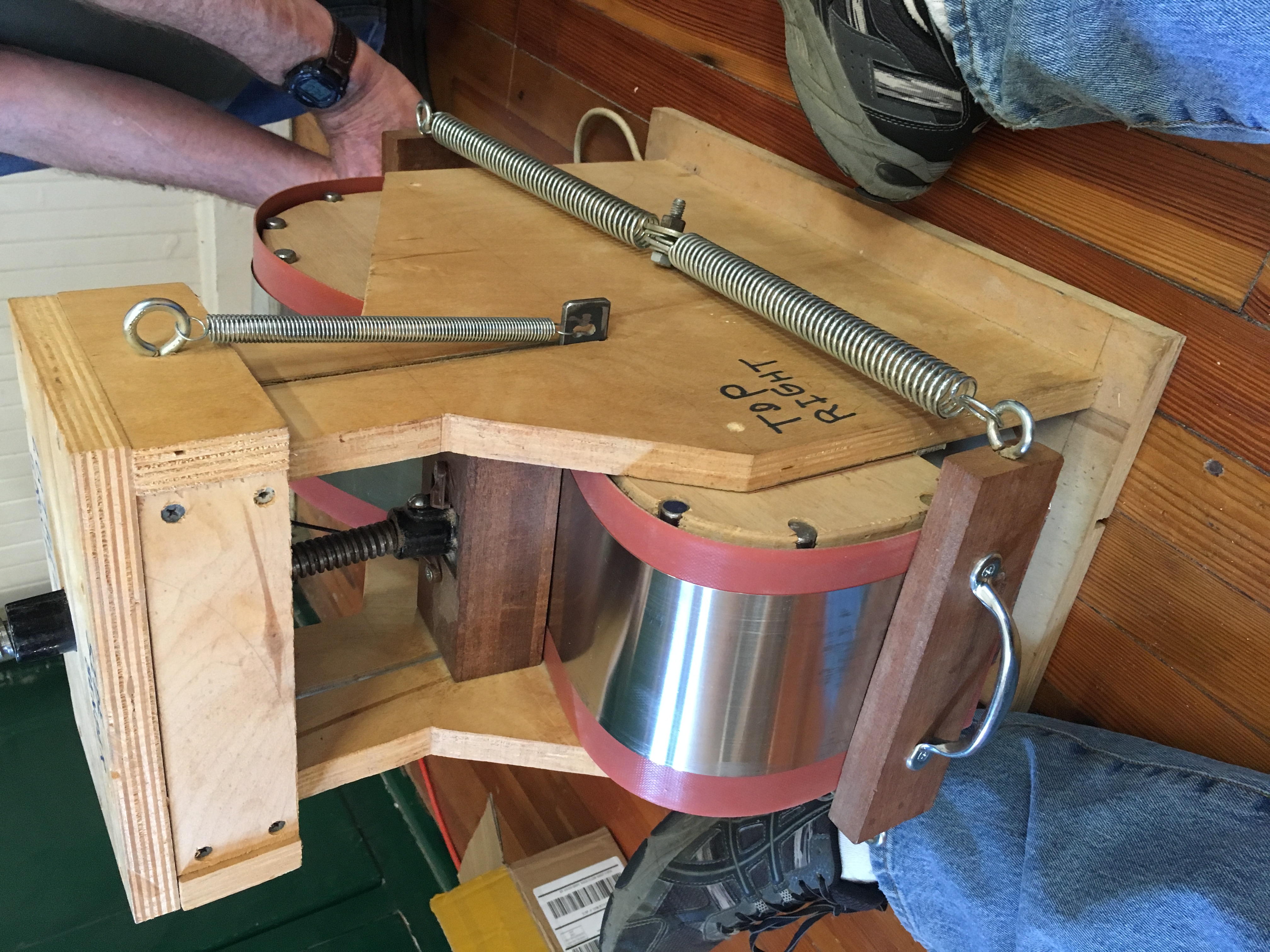